Assembly and testing has an important role to play at Sunfab
6/29/2016
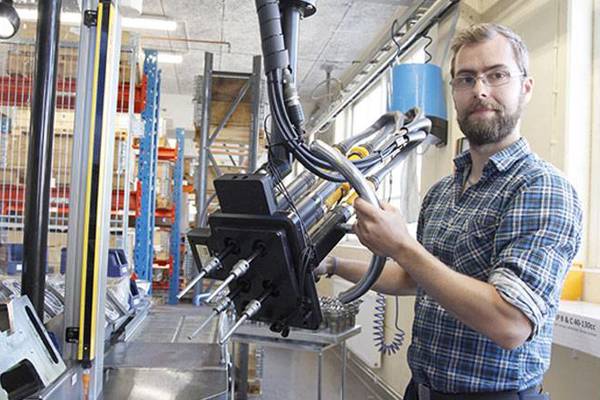
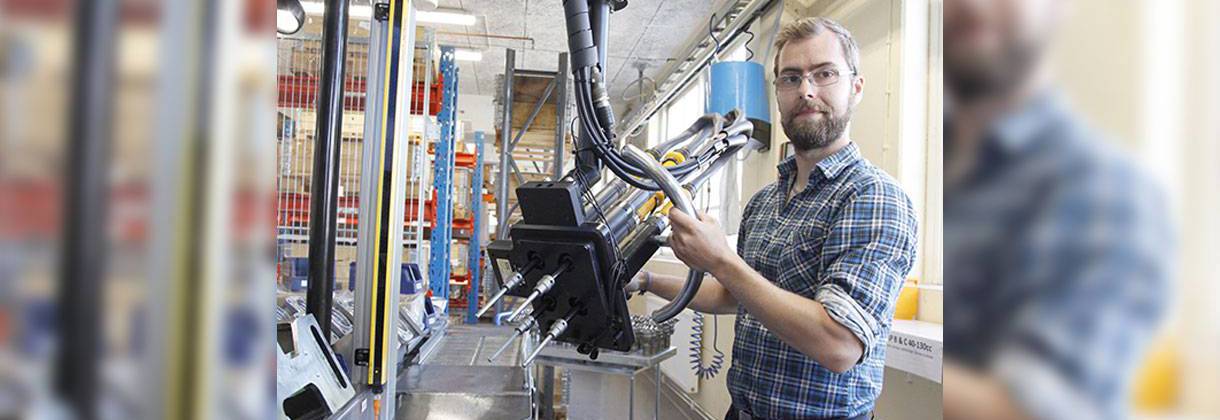
The department has an important role to play at Sunfab. Partly because all of Sunfab’s pumps and motors are assembled, but also because they are responsible for all the tests that are conducted.
The department consists of nine people working on six assembly lines and three test cells. The tempo is often high, depending primarily on how many orders are released and have to be delivered. Every morning, staff gather for a review of what is to be delivered during the day. As Sunfab strives to have a flat organisation with few middle managers, there is no department manager, there is instead a coordinator. The coordinator in the Assembly and Testing Department is called Björn Holmberg. As well as being a fitter, he is also responsible for staffing, capacity planning and the release of work orders. Staff rotate between the different workstations, giving them all broad-based competence and increasing flexibility in the department.
Always deliver on time
“My role as coordinator is largely about planning so that we in the department can deliver on time,” explains Björn Holmberg. “That’s why it’s important to maintain close collaboration with both back office and packing/dispatch so that, for example, we get information about any order that has priority and has to be delivered during the day. Even if things sometimes go wrong, we usually solve it somehow, because everyone in the department is incredibly focused on keeping to the delivery times we’ve promised. It’s not unusual for staff to come in and work on a Saturday, just to make sure that deliveries get away on time,” explains Björn.
Lasse Englund, fitter, in full flow assembling one of Sunfab’s motors.
Quality and ergonomics
“We work a lot on improving ergonomics and quality in the department,” continues Björn. “One example is the new investment in a multi-spindle screwdriver, which guarantees a precise tightening torque for the screw connections in the SAP range. As the pump is made of aluminium, it’s particularly important that we use a slow-tightening machine to achieve the correct torque. Other benefits of the new screwdriver are that it saves time, as it tightens all four screws simultaneously, and it also improves the ergonomics as it’s replaced a few monotonous work processes,” explains Björn.
Final testing
All pumps and motors that Sunfab manufactures are tested before delivery. In addition to this, there are continuous random checks on production in order to guarantee quality. These involve the product undergoing a test programme in which there are measurements of, among other things, flow and efficiency (both volumetric and mechanical), as well as flux loss at different speeds and pressure levels.
“We pressure-test all pumps and motors, after which all test results are saved in a database. As all pumps and motors have a unique serial number, they can then easily be traced,” concludes Björn Holmgren.
Faruk Kucukovic, fitter, spending the day pressure-testing pumps.